Repairs
Jenny Dowd
Things break.
Last fall I made a series of porcelain pendant light shades for the brand-new Jackson, WY restaurant, Picnic. It's not often I have the opportunity to make something for a public space, or that what I make is experienced by so many people. Picnic is a great spot, and has quickly become my favorite place to meet friends. And I have to admit, every time I see the cloud-inspired light formation I'm a little surprised.
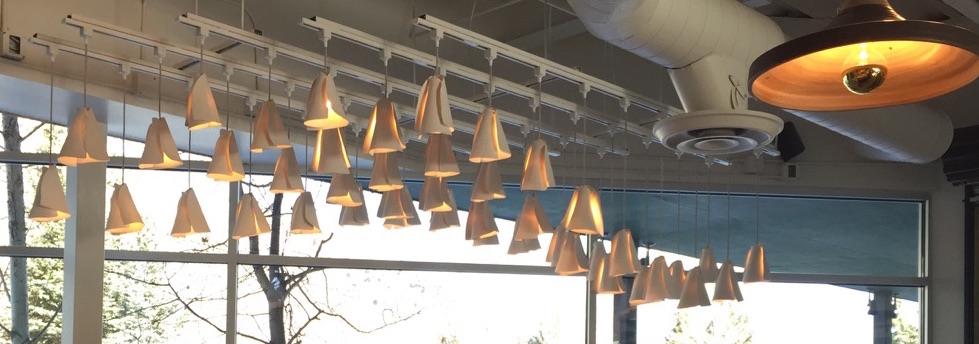
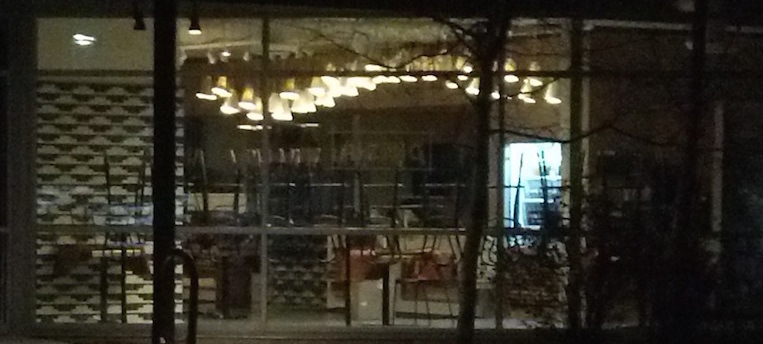
I will post an update soon with better photos of the installation.
I knew there was a possibility of a shade breaking, but I was still surprised when a tall person stood up with arms overhead and broke a low-hanging shade! I made a replacement, and this time, several extras.
Porcelain paperclay was perfect for this project. An addition of paperpulp to clay adds strength before firing- during which the paper burns out, making the form slightly lighter. The clay needed to be thin in order to be translucent; the forgiving nature of paperclay made these otherwise fragile forms possible.
This is my super high-tech process for making clay, a small batch made in my driveway.
Once the clay is dry enough to work with, I roll out thin slabs and cut the sides to shape using a template. I enjoy projects that push me to figure out interesting design solutions, in this case I needed to dry the clay into the shape I wanted, making sure the lightbulb fit inside without touching the sides of the shade. In this case, I made heavy-duty tarpaper cones and clamped them to a work table.
Another benefit of using paperclay is that wet clay can be attached to dry clay, this is something that usually ends in heartbreak. Once the sides were stiff enough to stand on their own, I attached a little clay to the top in order to change the shape.
Firing the fragile shades is tricky, I found that the two sides needed to be fired together so they would still fit together after possibly warping in the kiln. Not many fit on a shelf, and with their height the most I can get into my small kiln is 5.
While I had admired ceramic light shades I had never considered making them! I am glad for this challenge and the ideas that have been generated through trial and error. Now I'm looking at lights a little differently...